Norilsk Metallurgists to Independently Construct a Furnace
For the Nadezhgin Metallurgical Plant, located in the Norilsk Industrial District of the Krasnoyarsky Krai, plans are underway to self-manufacture an electrodessulphurization furnace, saving them hundreds of millions in rubles.
Electrodessulphurization furnaces are essential for processing slag from blast furnaces as well as converter slag, a byproduct of smelting ore concentrates. The furnaces extract residual valuable metals like nickel, cobalt, copper, platinum, and palladium from the slag.
Currently, the flagship company "Nornickel," Nadezhgin Plant, boasts four such furnaces, working 24/7 to process around 2,500 tons of raw material daily. The extracted valuable metals then go through further refining processes to produce finished products like refined nickel.
The efficiency of the furnaces significantly impacts the plant's overall production results.
Since 2022, engineers at the Mechanical Plant have been working on a unique, self-developed technology for manufacturing key elements — kessons — of the electric furnaces. A trial batch of these components, which require high precision, was successfully cast and installed during a major overhaul of the second technological line at NMZ in 2023. These components showed impressive results during testing, and plans are now in place to produce over 500 kessons with a total weight of over 100 tons.
By manufacturing these furnaces themselves, engineers can independently produce them, from casting to assembly, eliminating the need for external suppliers. This independence leads to savings of over 700 million rubles on the purchase of such equipment.
The new electrodessulphurization furnace is scheduled to go online at Nadezhgin Plant in February 2026.
Photo: "Nornickel"
Now, let's delve a bit deeper:
Economic Impacts
- Autonomy and Reliability: Producing crucial equipment, like electrodessulphurization furnaces, strengthens the plant's self-sufficiency and reduces the risk of supply chain disruptions.
- Cost Cutting: Manufacturing in-house can result in substantial savings in initial and ongoing costs, as the plant avoids procurement-related expenses including transportation and potential tariffs.
- Job Creation: In-house manufacturing may lead to job opportunities within the plant, supporting local employment and economic prosperity.
- Innovation and Adaptation: Self-manufacturing encourages innovation, as the plant can tailor-build equipment to suit its unique requirements and processes, resulting in more efficient operations and improved product quality.
Operational Process Benefits
- Customization: In-house manufacturing enables custom designs that perfectly align with the plant's operational needs, improving furnace efficiency and potential product quality and yield.
- Flexibility and Rapid Response: With in-house capabilities, the plant can swiftly respond to fluctuating production needs or repair requirements without facing delays from external suppliers, boosting overall operational flexibility and minimizing downtime.
- Quality Control: Manufacturing their own equipment provides the plant with control over quality standards, ensuring that their furnaces meet and surpass internal specifications, maintaining high-quality output.
- Technological Advancements: The in-house manufacturing process may also facilitate the development and implementation of new technologies or superior materials that enhance the efficiency of electrodessulphurization processes.
Financial Advantages
- Reduced Acquisition Costs: By forgoing expensive equipment acquisition from outside vendors, the plant significantly lessens capital expenditures.
- Lower Maintenance Costs: Custom-designed equipment can be optimized for ease of maintenance, potentially cutting ongoing maintenance costs.
- Increased Longevity: Equipment designed for specific use cases can enjoy extended lifespans if built to exacting standards, further reducing long-term operational costs.
In summary, self-manufacturing key components like electrodessulphurization furnaces at the Nadezhgin Metallurgical Plant offers cost savings through decreased purchase costs, reduced maintenance requirements, and elevated operational efficiencies. Additionally, it supports economic growth by generating local employment and fostering innovation.
- The self-manufacturing of electrodessulphurization furnaces by the Nadezhgin Metallurgical Plant, as planned, is expected to save over 700 million rubles in 2023, as they can independently produce the furnaces from casting to assembly.
- The new electrodessulphurization furnace, once operational in 2026, will boost the plant's production results significantly due to its efficient extraction of valuable metals like nickel, cobalt, copper, platinum, and palladium from slag.
- By producing the furnaces in-house, the Nadezhgin Metallurgical Plant can also enjoy cost-cutting benefits through reduced acquisition costs and lower maintenance costs, extending the lifespan of the equipment and reducing long-term operational costs.
- The autonomy gained through self-manufacturing enhances the plant's self-sufficiency, reducing the risk of supply chain disruptions, and fostering innovation by allowing for custom-designed equipment tailored to the plant's unique operational needs.
- In-house manufacturing may lead to job opportunities within the plant and support local economic prosperity, as the plant takes control of essential processes, from casting to assembly, without relying on external suppliers.
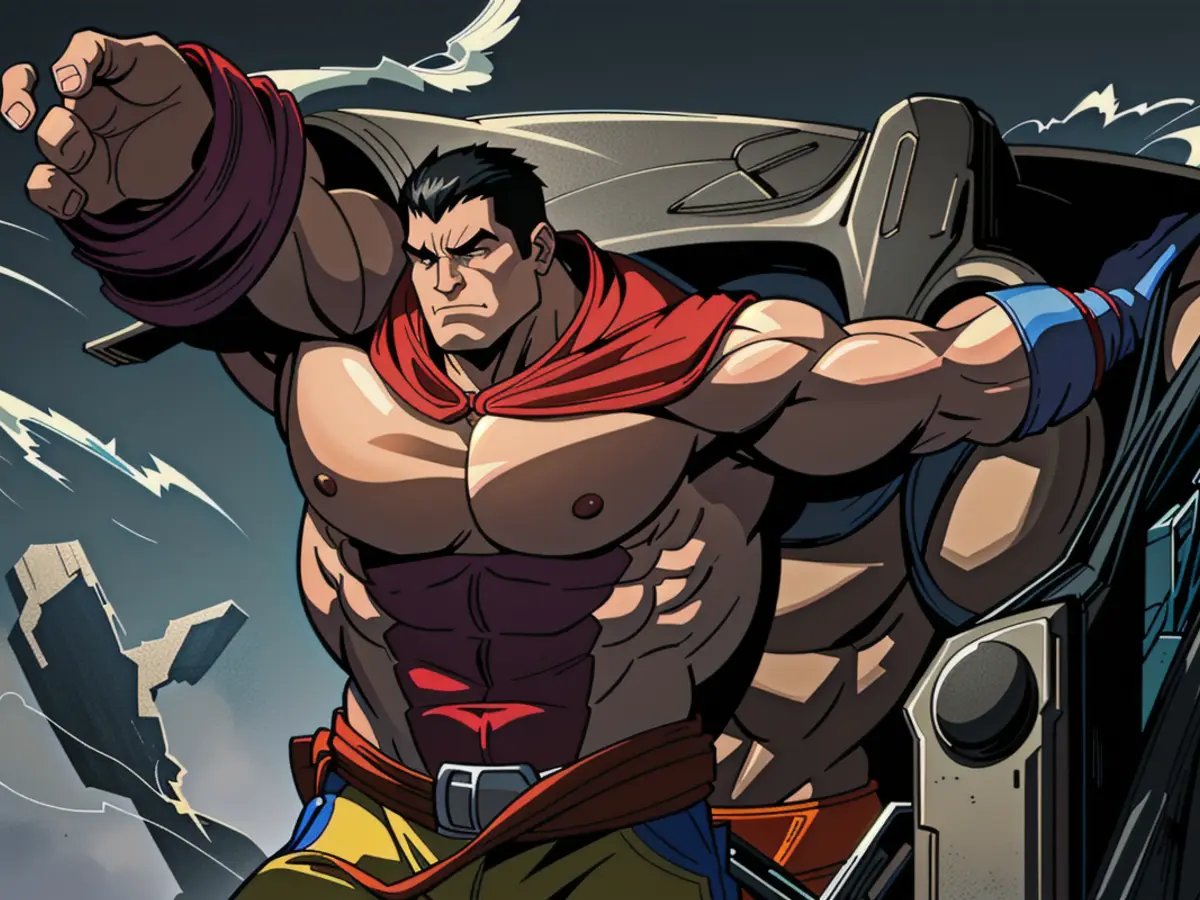